Prilling Units
High-end product quality, high production capacity, low energy consumption and minimal downtime.
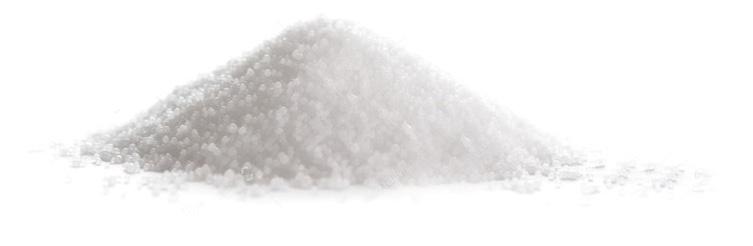
Full Package Overview
An overview of our full package for a prilled solidification section.
Prilling Tower
Inside the Kreber Prilling Tower, droplets are sprayed in a counter-current stream of the cooling medium to solidify the prills.
Prilling Scraper
When the prills have been formed and solidified, the Kreber Prill Scraper collects them in a slotted hole in the tower bottom.
Prilling Carriers
When the solidified and cooled prills are collected at the bottom of the tower, they need to be offloaded for packaging or further processing.
Prilling Medium
Prills are most often cooled in ambient air. Certain products can require an inert atmosphere, for safety reasons or because they react with oxygen.
Special Options
At Kreber, our aim is to consistently provide a safe and optimized prilling process. To this end, we have developed several special options.
Kreber Particle Technology
Particles have a wide range of applications, from pharmaceuticals to fertilizers. An application works best if the particles have the preferred structure, purity, size and shape. Kreber particle technologies are optimized to produce the particulate product with the right particle properties. Let us help you to develop the optimized technology for your particles.
Kreber designs, constructs, and supports
high-quality particle process technologies
for industries all over the world.
Nitrogen Fertilizer
Environmental Impact
And how Particle Engineering Profits the Planet.
The approach that can improve the fertilizers nitrogen use efficiency and counteract nitrogen pollution of the earth.
Fertilizer and Nitrogen
At the turn of the twentieth century, humanity was confronted with its biggest challenge up until that point: a global food crisis and subsequent mass starvation that loomed over the world. The global consumption of nitrogen compounds, be it in the form of nitrogen fertilizers or explosives, threatened to surpass its natural supply, in the form of natural niter and guano deposits. This challenge was solved by Fritz Haber and Carl Bosch with their novel process, which was capable of capturing atmospheric dinitrogen with hydrogen at high temperatures and pressures. Through this process, humanity became able to nourish the crops they were growing with the nutrient it needed the most: reactive nitrogen. In his Nobel lecture in 1920, Haber himself predicted that in the near future his process would be needed to produce millions of metric tons of fixed nitrogen [1]. He turned out to be right, as the world today produces over 100 Tg of nitrogen [2].
Impact of Fertilizers on the Environment
What Haber could not have foreseen was the environmental impact of fertilizer that the mass consumption of such a high amount of nitrogen compounds would have. As of now, the world is facing the opposite of the challenge it did at the end of the nineteenth century: battling the effects of nitrogen pollution on earth. However, this time there seems to be no one-stop solution to this looming crisis, and global collaboration is needed to change the way the world produces and consumes nitrogen-based fertilizers globally.
Kreber is active in particle engineering, a science that can help address the future challenges of reducing nitrogen pollution from fertilizers and therefore fertilizer pollution. This article will reflect on the possible ways particle engineering can improve the shaping and production of nitrogen fertilizers, and how that can help in overcoming the harmful effects of this global challenge.
A Global Challenge: Optimizing the Nitrogen Fertilizer Cycle
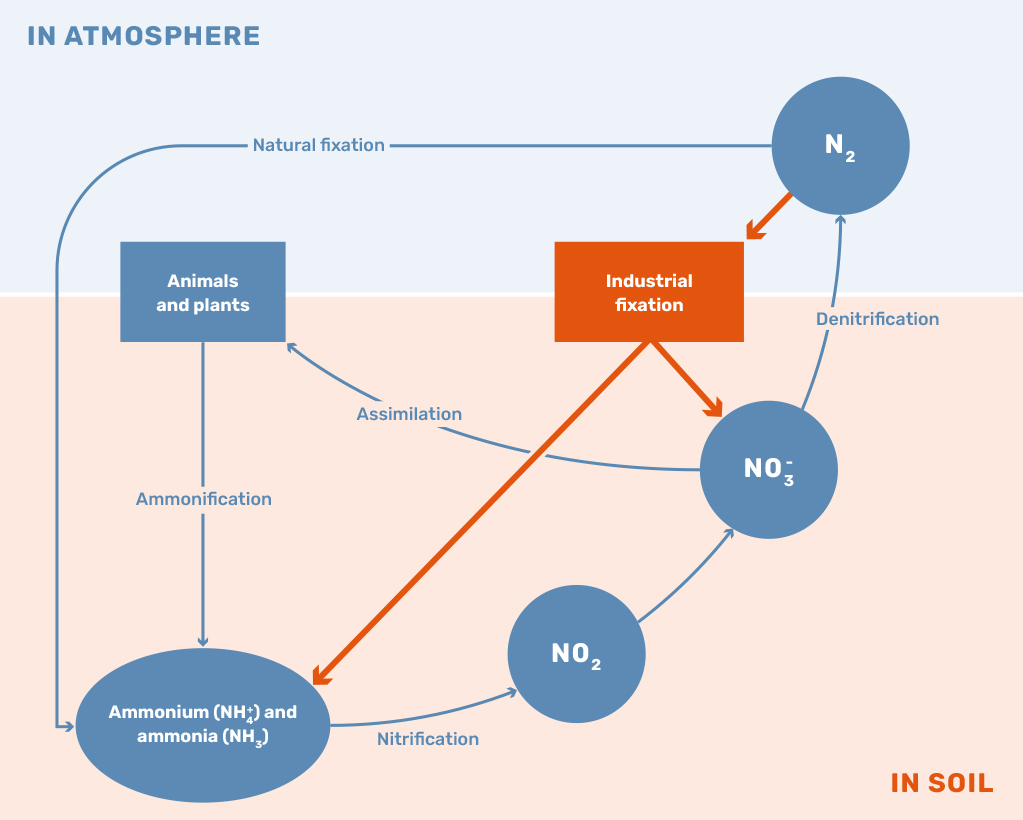
While the application of nitrogen-based fertilizers is still vital to sustaining the current population, the surplus of nitrogen leaking into the environment is leading to numerous concerning developments. The current method of using and producing nitrogen fertilizers has led to reductions in biodiversity and the acceleration of climate change through the production of nitrous oxide, mainly driven by an imbalance in the nitrogen cycle, as shown in Figure 1. The global challenge the world is currently facing can be described as the problem of maximizing the net positive outcomes of all available nitrogen fertilizers.
As suggested by Houlton et al, making the most of these benefits lies in the development of the following five strategic imperatives [3].
1. Increasing the efficiency of nitrogen use
Nitrogen use efficiency is defined as the nitrogen that will end up absorbed into the crops over the total nitrogen applied in the form of fertilizers.
Counter-intuitively, research has shown that over the last century, efficiency has actually decreased from 60% down to approximately 46% [3]. Efficiency improvement can be achieved by focusing on the 4R’s of good nutrient stewardship: Right source, Right rate, Right time, Right place [4].
The ‘right source’ means that the fertilizer type or nutrient content is matched to the specific needs of the crop to which it will be applied, while the ‘right rate’ focuses on the ideal amount of nutrients that is tailored to the crops’ exact needs. The ‘right time’ or timing means that the relevant nutrients are made available at the ideal moment that the crop needs them. Finally, the ‘right place’ or placement means that the nutrient is placed where the crop can easily consume it.
2. Getting nitrogen to where it is needed
While there is an abundance of affordable nitrogen fertilizers in wealthier nations, there are still countries with only limited access to them. Improved accessibility will increase resilience to negative weather effects and lower the likelihood of worldwide famine, as long as the nitrogen is applied in an efficient and low-polluting manner.
3. Removing nitrogen pollution from the environment
In order to reduce the unwanted effects of nitrogen pollution, leaked nitrogen can be removed from the environment by either agro-ecological or technological methods. These two removal methods also bring with them the possibility of potentially recycling the nitrogen and increasing nitrogen use efficiency, thus lowering the environmental impact of fertilizer in the long run.
4. Reducing food waste
At a governmental, industrial, social and individual level, spillage and overbuying both lead to the fact that approximately a quarter of all food is wasted along its lifecycle, rendering a significant quantity of applied nitrogen fertilizer unused in terms of nutrition.
5. Encouraging diets with low nitrogen footprints
Lastly, dietary choices have consequences for both the environment and individual health. For instance, approximately 10% of all nitrogen used for the production of cow feed for beef production is lost in the process. Lifecycle analysis and consumer education will be required to guide consumers to a smaller footprint.
Particle Engineering
One method of overcoming these challenges lies in the field of particle engineering. Particle engineering is the science of altering or forming solids into a desired shape, size distribution or composition, and is also concerned with other aspects of the particle’s morphology and surface characteristics. This type of engineering is mainly applied in the fields of pharmaceuticals, food, cosmetics, and paints, where the morphology of particles is handled with the utmost care.
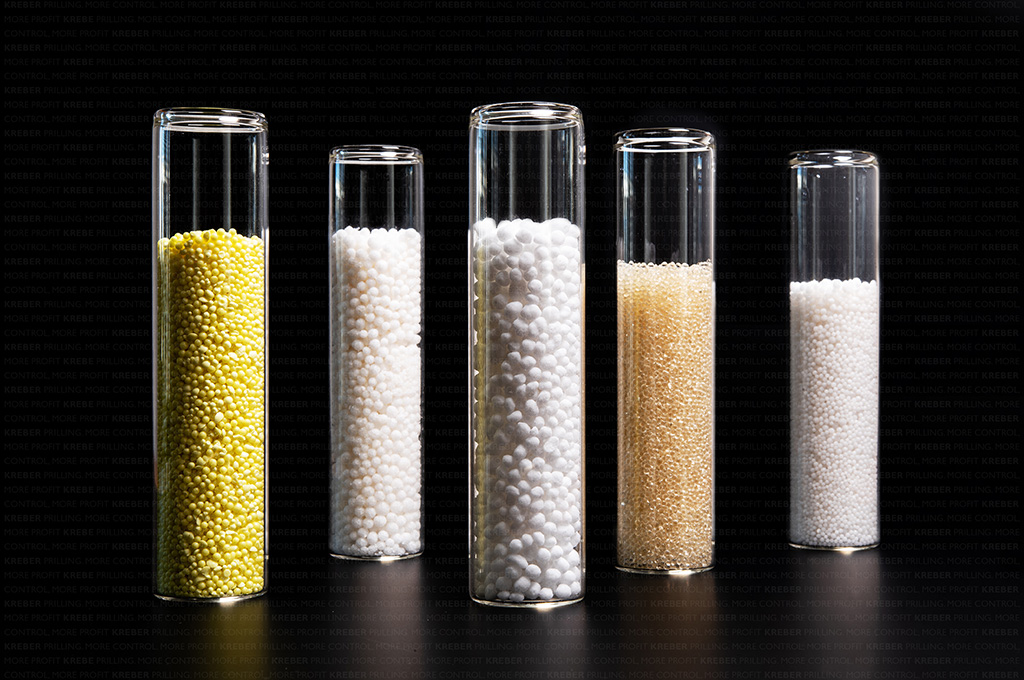
Prilling
Prilling, the core technology of Kreber, is a method of particle engineering for spherical solids in the range of approximately 0.5 to 3 mm, as shown in Figure 2. In-depth particle engineering can have an effect on several physical aspects of spherical solids, such as:
- Solubility and/or dissolution behavior
- Flowability (free-flowing)
- Homogeneity and stability against segregation
- Dose uniformity
- Bulk density
- Stabilization of mixtures
- Hygroscopicity
For instance, in milk powder production – which is achieved by spray-drying – particle engineering is widely used with regards to dissolution behavior. For the consumers, food powder dissolution has a direct impact on their perception of the overall product quality. By altering the size, shape, and porosity – whilst maintaining the important flavor characteristics – solubility is greatly increased. Before particle engineering was applied in the production of milk powder, adding the finished product to water would result in the powder floating on the top of the liquid. The powdered milks of today readily fall to the bottom of the water, resulting in a fast-dissolving powder.
Use in Practice for Nitrogen Fertilizers
In terms of the five solution directions discussed in the previous section, the science of particle engineering can play a role in improving the efficiency of nitrogen usage. More specifically, when applied to the 4R’s, it helps to improve the right time and right place solutions.
For the first solution (the right time), the timing of consistent nitrogen release can be coupled, among other variables, to the dissolving rate of the nitrogen source. Nitrogen release is achieved either by water dissolving the nitrogen or by bacterial life-transforming the fertilizers’ nitrogen into nitrites that are essential to the crop. The available surface area can be adjusted through particle engineering by ensuring a specific particle size or porosity, or by applying a coating or encapsulating the nitrogen source.
Currently, particle engineering solutions are already being explored in order to achieve a controlled release rate. For instance, ammonium nitrate in its more porous low-density form has an accessible surface area that is approximately five times greater than ammonium nitrate in its high-density form [5]. As the surface area can be coupled to the dissolving rate, a dissolution rate decrease of up to five times can be achieved when porosity is minimized. Subsequently, when the high-density form of ammonium nitrate is encapsulated, the nitrogen release rate can be altered even further. In urea fertilizers, the application of coating urea prills with slowly dissolvable sulfur or a polymer has led to a clearly slower release rate, with the added benefit of sulfur as an additional nutrient for the crops.
In pharmaceutical applications, when the control rate is of the utmost importance, encapsulation is the most common approach. There, a carrier melt is used in which the active compound is suspended. The melt is subsequently either spray-chilled or prilled in order to arrive at a solid material with the active compound encapsulated. The carrier melt dissolution characteristics, coupled with the active compound concentration and compound size relative to the final product, can be altered accordingly to accurately obtain the desired release rate of the active compound. A similar type of process can be explored for nitrogen fertilizers as well, where either urea or ammonium nitrate powder can be suspended in a wax or other slowly dissolving, bio-friendly compound, in order to gain control of the release characteristics.
As for the second solution, the right place, it is important that the nutrients are delivered at the place where the crops need them. Currently, consistent particle size is of importance for the traditional mechanical method of distributing fertilizers over farmland.
Using Liquid Fertilizers
Newer methods of fertilizer distribution have shown the potential of using liquid fertilizers in bulk to obtain better control of the dose uniformity over the crop fields. This liquid fertilizer would consist of either slurries (solids suspended in a liquid) or a solution of nutrients in an environmentally friendly liquid. The liquid nature of these nitrogen fertilizers means that the nutrient can be sprayed evenly over the land, leading to a high degree of control over the dosage per square meter and therefore over the placement of the nutrients.
The way slurries or solutions are created will yield a need for different and more flexible technological designs for applications with nitrogen fertilizers. When directly supplied to the crops, the nitrogen release rate needs to match the needs of the crop and the land it grows upon. When used to create a liquid fertilizer, however, where the solid will be dissolved or suspended in a liquid, the particle size has to be much smaller to be able to accurately dose and quickly dissolve the fertilizer in the carrier liquid.
Conclusion
Fighting the pollution effects of nitrogen fertilizer use, while still having the means to help feed all of humanity is a truly daunting challenge now, just as it was in the late 1800s. This time, however, it is not an option to wait for a singular, brilliant solution such as the Haber-Bosch process. Industry-wide joint initiatives are essential, coupled with a level of decisiveness from governments all over the world to tackle these problems. Smarter ways of offering nitrogen fertilizers to crops is one of the main issues on which a better method has to be found to increase the nitrogen use efficiency, while also reducing the fertilizers’ environmental impact. In that light, particle engineering can prove to be a piece of the puzzle, which has to be solved together.
References
- Haber, F. The synthesis of ammonia from its elements. Nobel Lecture, 2 June 1920
- Heffer, P. and Prud’Homme, M. Global nitrogen fertiliser demand and supply: trend, current level and outlook. Paper given at the 7th International Nitrogen Initiative Conference, Melbourne, Australia, December 2016
- Houlton, B.Z., Almaraz, M., Aneja, V., Austin, A.T., Bai, E., Cassman, K.G., Compton, J.E., Davidson, E.A., Erisman, J.W., Galloway, J.N., Gu, B., Yao, G., Martinelli, L.A., Scow, K., Schlesinger, W.H., Tomich, T.P., Wang, C., and Zhang, X. A World of Co-Benefits: Solving the Global Nitrogen Challenge. Earth’s Future, Vol. 7, No. 8, pp. 865 – 872, August 2019.
- Flis, S. 4R history and recent phosphorus research. Crops & Soils, Vol. 51, No. 2, pp. 36 – 47, March – April 2018.
- Zygmunt, B., and Buczkowski, D. Influence of Ammonium Nitrate Prills’ Properties on Detonation Velocity of ANFO. Propellants, Explosives, Pyrotechnics, Vol. 32, No. 5, pp. 411 – 414, October 2007
Prilling Machine
Forming technology for processing plants.
Over the years, we have built up an impressive track record in manufacturing prilling machines.
The first fertilizer prilling machine we built in the 1960s is still in operation today and continues to deliver a positive cash flow for our client. The proof of this track record is our ever-growing prilling reference list.
Prill Formation Possibilities
Explore which method of prilling meets your requirements.
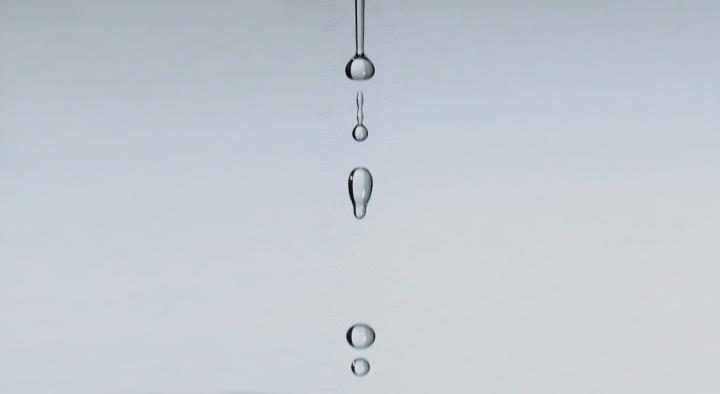
Static Prilling
We offer the Kreber Static Prilling System for the conventional method of prilling. This type of system can contain one or more prilling heads and is very suitable for capacities ranging from 5 to 500 metric tons/day.
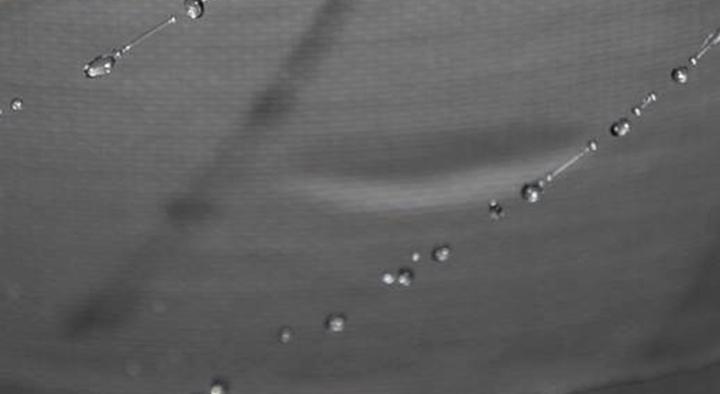
Rotary Prilling
The Kreber Rotary Prilling System has two rotary prilling buckets. This allows for quick changeover of prilling buckets, thus ensuring continuity of production. This type of system is suitable for capacities ranging from 75 to 5000 metric tons/day and comes in a number of standard models to which various applications can be flexibly added.
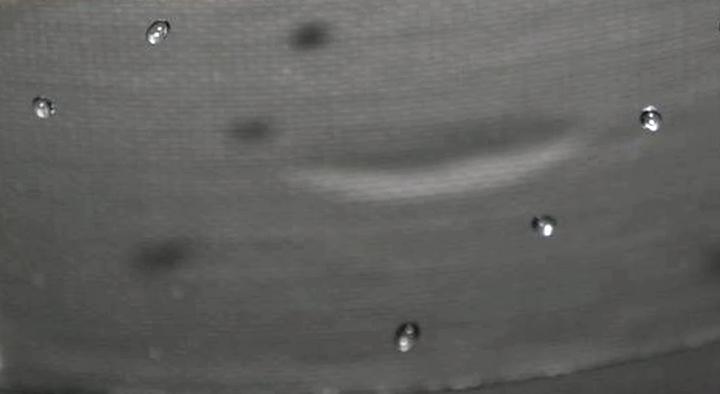
Vibro Prilling
Thanks to our innovative facilities, the R&D team is able to take prilling technology and customer solutions to the next level. One of our major developments is ‘vibro prilling’. Applying vibration to the melt results in more uniform prills with a narrowly defined prill size distribution. This principle can be applied to both static prilling and rotary prilling.
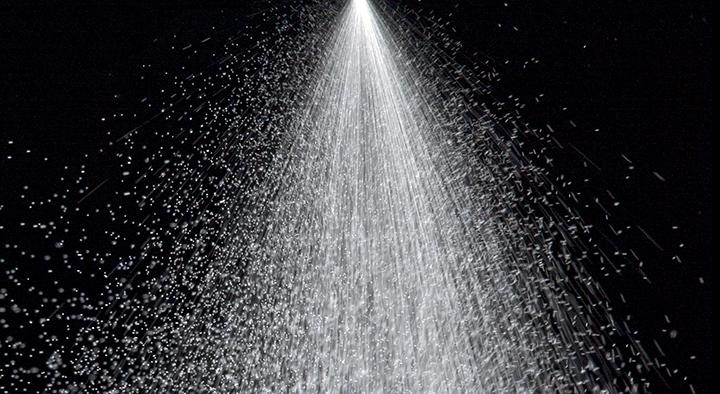
Microprilling
Microprilling (also sometimes referred to as spray cooling, spray congealing or spray chilling) is a technique that uses an atomizer to create a cloud of fine droplets. The resulting particles from this cloud are very small (D50<0.5mm). Due to their perfectly spherical shape these particles still earn their right to be classified as prills, rather than just a powder.
Meaning of Prilling
The Main Principles of the Prilling Process and the Definition of a Prill.
Prilling is an extremely effective finishing technology and offers many advantages over other solidification methods. But what is prilling? And what is a prill? To define prilling, we need to examine both the main principles of the process and the end product. But before we do this, let's go back to where it all started...
Invention of Prilling
Legend has it that one night in 1782, William Watts, a plumber from the city of Bristol in the UK, was walking home after a night of drinking ale in the local pub. Along the way, he decided to take a rest near the St Mary Redcliffe Church, the lead roof of which he had recently renovated. As he lay on a bench, worrying about his wife’s disappointment alone home alone, he drifted off into a dream-filled sleep.
In his dreams, his wife's anger kept haunting him. He saw her towering over the church and, in her anger, she poured molten lead down the tower onto his face. The lead didn't form a stream but instead shaped into perfect spherical balls. He woke up to find that it was only the Bristol rain falling from the sky.
The next day he decided to experiment and, together with his wife, climbed the spiral stairs up to the church’s roof. They drilled holes in the bottom of a pan, melted some lead, and fed it through the holes. Just like in the dream, the molten lead formed spherical droplets, which solidified into perfectly spherical (definition of prill) lead balls before hitting the ground. These balls became known as patent lead shot, which was used in shotguns designated for hunting [1].
Previously, lead shot was produced according to a slow and laborious molding process, giving irregularly shaped and expensive lead balls. Watts, a keen hunter himself, was so convinced of this production method that he decided to build the world’s first prilling tower, right on top of his house [2].
Until this day, spherical products from the chemical industry are produced in very much the same way as it was invented by William Watts; currently known as the process of prilling.
What is Prilling?
Prilling is a shaping or finishing technology which is widely applied in the chemical industry. The process of prilling physically changes a molten stream of a product into solidified spherical particles, called prills, with a size between 500 and 4000 micrometers. In general, the prilling process consists of three main components; The prilling machine, the prilling tower, and the cooling medium.
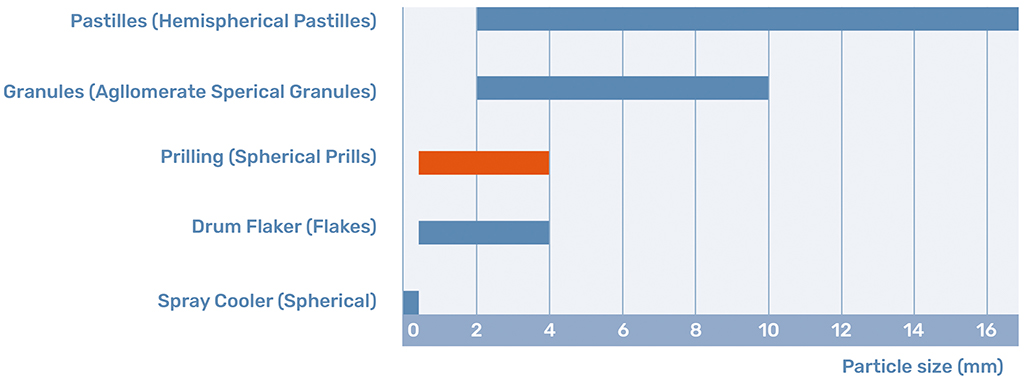
Prilling Machine
The prilling machine is the location where the prill is formed. The melt is formed in a jet by the prilling machine, which subsequently breaks up into droplets. The droplets that are produced solidify into the prills.
The formation and breakup of a liquid jet are governed by the physical properties of the melt. Therefore, each new prilling facility has to be designed in accordance with the material that needs to be prilled and the customer’s preferred size of the produced prill.
Prilling Tower
The droplets formed by the prilling machine solidify in the prilling tower. A prilling tower is operated with a gas stream of the cooling medium to cool the prills. The gas stream can be operated in two different ways; a countercurrent or co-current flow. The most common is the countercurrent flow since this operation allows the residence time of the prills in the tower to be increased and also gives better heat distribution over the tower.
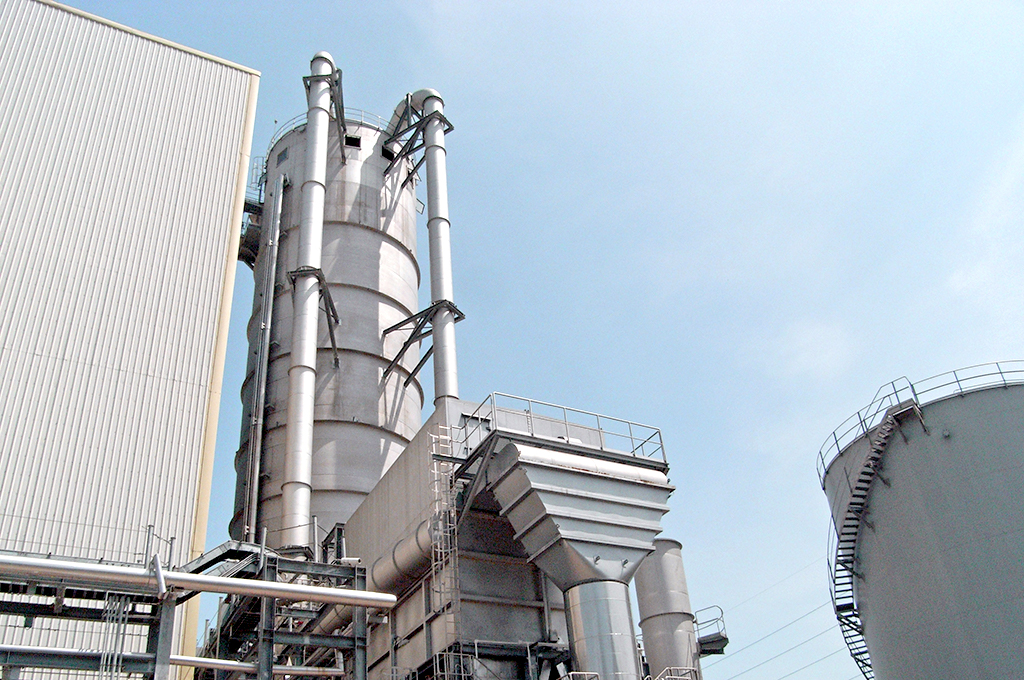
The different melts and the different particle sizes that are prilled require different tower heights to make sure the droplets are completely solidified before they hit the bottom of the prilling tower. Prilling towers can be everything from 20m up to more than 60m in height and are usually constructed from either cement or steel, depending on the melt and how corrosive it is.
At the bottom of the tower, the prills need to be collected and sent to packaging. A scraper is placed at the bottom, which gently pushes the prills to a screw conveyor that transports the product to big bags.
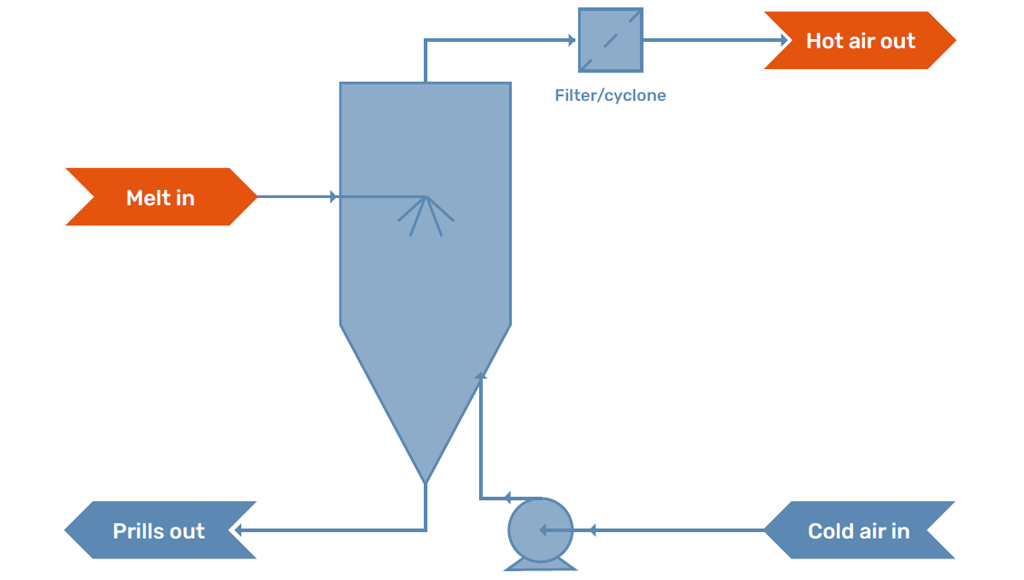
Cooling Medium
In the prilling tower, the droplets formed by the prilling machine are in contact with the cooling medium. Traditionally, prilling towers operate with an airstream in order to cool and solidify the prills. The air stream is either caused by natural draft, as a temperature difference will develop over the tower, or is influenced by a fan which creates and controls the flow.
There is always some dust formation inside a prilling tower. This formation can be due to evaporation, satellite droplets, or because parts of the prills break off on impact with the floor. Modern prilling towers are therefore equipped with a filter package to capture the formed dust and either reuse it in the process or package it as a separate product stream.
Next to the traditional air prilling towers, recent innovations have made it possible to use other cooling media, such as nitrogen, in the prilling process. This innovation is known as closed-loop operation and allows the cooling medium to be reused in the prilling process, eliminating dust emission into the environment.
The use of nitrogen ensures safe prilling of a whole new range of molten products, which are highly sensitive to dust explosions. This hazard was one of the reasons why the prilling industry stopped producing sulfur prills. Research at Kreber has shown that with our current innovations, this will possibly change in the near future. For more information about our most recent developments, please read the following article: sulfur formation and solidification technologies.
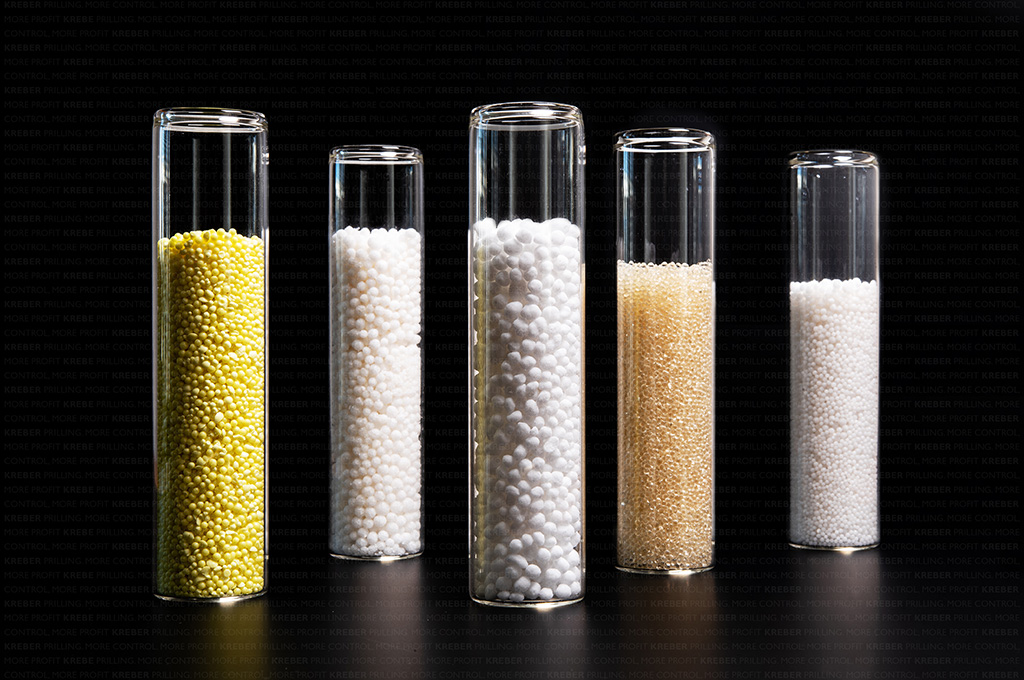
What are Prills?
Prills are the product of the prilling process. Prills are defined by their spherical shape and their size between 0.5 and 4 mm. This shape and size determine that the prill is a free-flowing product with certain distinct benefits.
The spherical shape of prill is preferred when a product needs to be free-flowing. A prill on a slightly inclined surface will already start rolling, making it easy to handle as a product. The size yields a product that is easily dosed but is not a dusty product, limiting product losses and maintenance costs.
Prills are widely applied in the fertilizer industry, as the size enables farmers to mechanically distribute them evenly over the soil. In addition, products with a high dust explosion risk are finished into a prill to limit that risk, as prills are larger than dust (< 500 mu). This is the case in BPA prilling, for instance.
Future of prilling
Even though prilling has been around for centuries, it is still evolving. While prilling was already a good choice for any market wanting a robust finishing method for their material, new innovations are in the works to improve and streamline the process even further.
An excellent example of a new innovation in prilling is a closed-loop system, where the cooling gas is reused after leaving the tower. Environmental emissions are reduced to practically zero and the safety of the operational process is significantly increased. Upcoming developments are the mitigation of the satellite droplet formation, which will also optimize the prill size distribution. These innovations make the prilling process a better alternative, compared to the other main finishing methods.
Major Benefits
Prilling is often the most preferred method because it offers the following advantages over other solidification methods:
- Most Cost-Effective
Prilling is one of the most economical finishing technologies in the world for large outputs. Compared with other solidification methods such as granulation and pastillation, CAPEX and OPEX are several times lower at increased capacities.
- Highly Flexible
Prilling production is easily scalable within the range of 70 to 110% of the originally designed capacity. This makes the prilling production method an extremely flexible option for your total production process. The prilling process is also easily scalable in its throughput, making it an interesting alternative for companies looking for small batch
- Guaranteed Continuity
The high degree of ‘self-control’ makes prilling a robust finishing technology with a very stable processing procedure. It can therefore play a vital role in guaranteeing the continuity of your process and quality of your product.
- Energy-Efficient
The process requires minimal energy consumption. In fact, it is the most energy-efficient solidification technology available. This helps you minimize your operational expenses.
- Convenient Operation
Our equipment is easy to operate thanks to our well-defined process operating parameters. Furthermore, the limited rotation and intricate parts result in a reliable process, giving the client low overall operational and maintenance costs.
- Small Footprint
With the design of our prilling tower and additional equipment, you benefit from a relatively small footprint in comparison to other solidification technologies.
- Emission-Compliant
Thanks to a constant stream of technical innovations, such as state-of-the-art air inlet filtration and scrubber technologies, prilling has evolved into a cleaner finishing technology than it has ever been.
References
- Harrison, David. Dream Lead to Invention. Bristol Times, November 26, 2002.
- Watts, Williams. Small Shot. 1347 United Kingdom, December 10, 1782.
Solidification:
Sulphur Forming
About the Sulphur Production Process, Prilled Sulphur and Future Developments.
Regarding the sulphur manufacturing process, prilling molten sulphur has been done in the past. However, due to some unfortunate events, prilling sulfur was discontinued in the industry. Recent developments have changed this perception, and the possibility of prilling sulfur is being looked at once again as a possible high throughput alternative to other sulphur finishing processes. The goal here is to educate the reader on the current state of sulphur forming technologies and where prilling fits in as an alternative.
The Discovery of Prilling
Back to Where it All Began
The inventor of the prilling method was a plumber from the UK named William Watts. In 1782, he discovered that by letting molten lead flow through a small orifice and fall from an elevated height, that on the way down, the lead drops would solidify and form spherical pellets.[1] These pellets would be similar in size and more spherical than most of the current production methods at the time.
The basic principle behind the prilling process has not changed much since William Watts discovered it in 1782.[2] The main differences are that today a prilling machine is used where large amounts of liquid jets are produced by forcing the melt through a nozzle which then breaks up into small droplets. This sulfur solidification unit or sulfur forming unit provides better control of the jet break-up and in turn better quality and size of the product. Additionally, air can flow through the tower and dust can be collected by filter installations or with the use of scrubbers making operation safer.
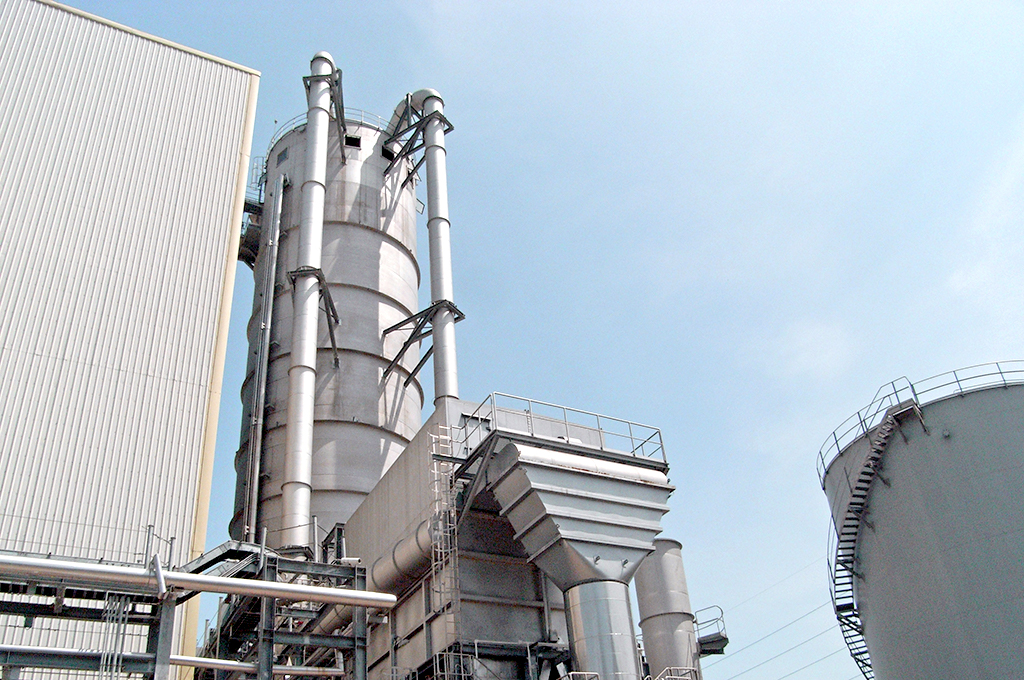
The main markets for prilling are the fertilizer market and plastics finishing. Prilling is the preferred finishing method when high throughput and stable operation is required. Prilling also offers flexible operation and narrow particle size distribution (PSD) compared to other finishing methods. The marketplace for prilling is expanding as the technology matures and new innovations are realized.
Prilling of Sulfur
In the world of sulfur, converting molten sulfur into large quantities of solid particles has always been a challenge. Crushing a solid block of sulphur into smaller chunks was utilized as the main method of obtaining transportable sulfur pieces. Due to considerable dust formations while handling solid sulfur pieces in this form, the industry started looking for new technologies to form their product.
One of the adapted technologies was air prilling, which was already utilized by the fertilizer industry. The finished product from these prilling facilities were large quantities of small yet perfectly spherical pellets with a polished surface and a relatively narrow PSD, leading to a free-flowing product. At this point, when prilling was the most dominant method of producing solid sulfur, the well-known SUDIC specification (Sulphur Development Institute of Canada) was also made, leading to a market standard for all sulphur technologies.
Nevertheless, the industry developed new ways of production, such as sulfur granulation process, (steel belt) sulphur pastillation and wet prilled sulphur, which took over the role of being the most dominant method of particle engineering in the sulfur industry.
Two Main Concerns
This shift in production method was the result of two main concerns.[3] Firstly, the prilling towers designed in the ‘60s operated on an open-air design. This means that all cooling air used for solidifying the prills is immediately ejected into the environment. All the dust particles formed during the prilling process, but also any vapors from the sulfur melt, is taken with the air stream into the environment. This led to environmental problems in the downwind areas of the prilling plant.
Secondly, a disastrous fire incident in the Middle East led to the conclusion that dry prilling in itself was to be considered a high-risk technology.[4] The low ignition energy, combined with the potential buildup of static charge in the solidifying prills, can lead to dangerous sparks. The combination of these two aspects, coupled with a hot climate, led to the disastrous incident in the Middle East.
Safer and More Sustainable Future
In the last few years, prilling has been under development to handle a wide variety of products. The addition of an air treatment section was applied in the late 80s, where either a dry filter or wet scrubber is utilized to drastically cut down on (dust) emissions from prilling towers. However, as the environmental impact of all industrial plants on their surrounding became more apparent, the laws became more and more stringent on the prilling production. This resulted in a surge of new research on prilling, with a closed-loop process as one of the main achievements.
Closing the Loop
For the closed-loop process, the used cooling medium (in this case air) is first led to an air treatment section, and afterwards to a heat exchanger. The resulting cleaned and cooled air can be reused in the tower. The main benefit of closing the loop is the fact that emissions are reduced to zero. Next to that, the cumulated heat removed from the cooling medium can be reused somewhere else in the plant, leading to a higher degree of heat integration of the total plant.
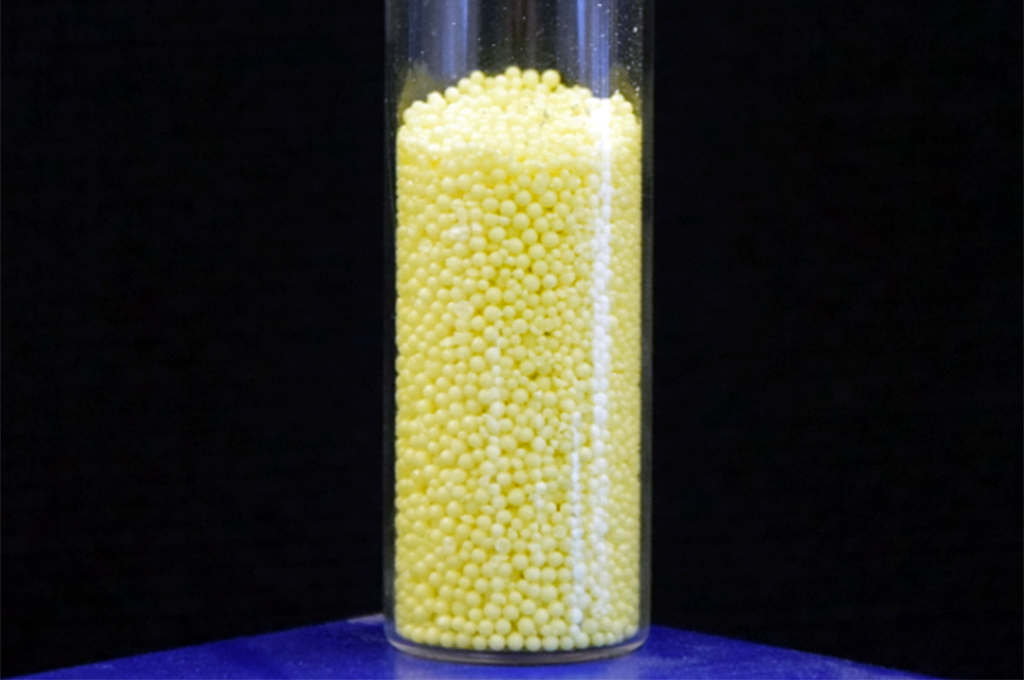
Safely Handling Sulfur
Prilling is already widely applied in other industries, where the same hazards with regard to fire and dust explosions exists, mainly near the air treatment section. When applying the closed-loop principle, all of the cooling medium is recycled, removing the necessity of having to use ambient air as a cooling medium. Practically any gas can be chosen because the waste of the cooling medium will be very limited. Currently, the first prilling towers with the inert nitrogen gas as a cooling medium have started to emerge, leading to an intrinsically safe method of prilling with no emissions and low fire hazards.
These prilling towers form a safe and high capacity production method of converting melt into a preferable finishing product. These innovations are showing promise in the field of sulphur as well. It is already empirically proven that sulfur prills can be formed and that they have a range of benefits over other sulphur solidification technologies. The main challenge now is to alter the closed-loop prilling system as is used in the world of plastics and fertilizers prilling, towards a system that can safely handle sulfur.
Future Developments
From the first days in 18th century rainy Bristol until now, prilling has gone through a lot of developments. The latest innovations are mainly in the off-gas section and a higher degree of control on the total process, which have led to a safe and trustworthy process to create prills from a melt. Prills still have their unique product qualities over the other product of the other main forming technologies.
Currently, the main challenge is to find a way to prill sulphur in a safe and economical way. Closed-loop prilling with inert cooling medium shows a great promise to make this achievable. There are still a handful of challenges to overcome before this stage is reached, challenges that will demand all the know-how and vision that a company can muster. Kreber is more than willing to pool their resources with any interested party in order to reach this ideal prilling process that will result in benefits for all involved, whether economically or environmentally. Because, in the end, even William Watts couldn’t make the first prilling tower on its own, he needed a helping hand from his dream wife.
References
- Harrison, David. Dream Lead to Invention. Bristol Times, 26 November 2002.
- Watts, Williams. Small Shot. 1347 United Kingdom, 10 December 1782.
- D’Aquin, Jerry. Davis, Paul. Formed Sulphur specification guidelines: SUDIC, 40 years following publication. Sulphur magazine, October 2018
- Kent, J.A. Kent and Riegel. Handbook of Industrial Chemistry and Biotechnology, Springer Science & Business media, 2010
The Differences between Prilling and Granulation
Breakdown and Comparison of two Major Finishing Technologies.
The choice of the right solidification technology can be the deciding factor. Not only for investment costs or operational expenses but also for the consistency of your product quality. With the right insights, you can make the right choices. This is why we will be comparing two major finishing technologies: prilling and granulation.
Introducing the Technologies
Prilling: Back to Where it All Began
The inventor of the prilling method was a plumber from the UK named William Watts. In 1782, he discovered that by letting molten lead flow through a small orifice and fall from an elevated height, that on the way down, the lead drops would solidify and form spherical pellets.[1] These pellets would be similar in size and more spherical than most of the current production methods at the time.
The basic principle behind the prilling process has not changed much since William Watts discovered it in 1782.[2] The main differences are that today a prilling machine is used where large amounts of liquid jets are produced by forcing the melt through a nozzle which then breaks up into small droplets. The priller provides better control of the jet break-up and in turn better quality and size of the product. Additionally, air can flow through the tower and dust can be collected by filter installations or with the use of scrubbers making operation safer. For more information about the main principles of prilling, please read the following article: prilling meaning and prill definition.
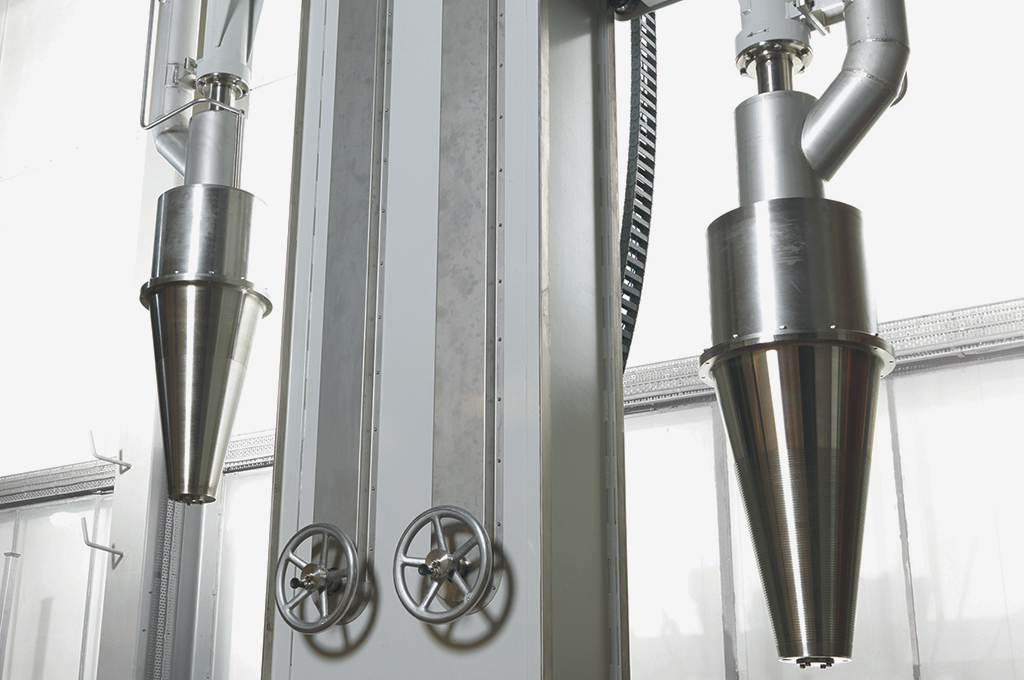
Granulation: Promising Technology
In recent history, granulation technology emerged as a promising technology for manufacturing high-grade fertilizer. Discovered in 1965, the ammonium granulator was patented by Frank Nielson. Nielson worked within the Tennessee Valley Authority which partly evolved into the International Fertilizer Development Center. The work done by the TVA resulted in a competitor for prilling in the large-scale finishing of Chemical Fertilizers [3].
In the granulation process, small particles are bound together to create granules. Both melt and a binding agent, are fed as a mist of small droplets into the granulator. Small seed particles feed on the mist of droplets until the desired granule is formed. The rotating drum and high air velocities allow for efficient wetting, drying, and energy transportation.
After 50 years of innovation in the field of granulation and more than 200 in the field of prilling, both technologies have evolved into mature finishing technologies that are operated around the world. But after all these years of research and development, is it possible to make a distinction between the different products? And what are the benefits and drawbacks in the process of both state-of-the-art prillers and granulators? Lastly, what can both technologies learn from each other to move towards a better practice of finishing fertilizer?
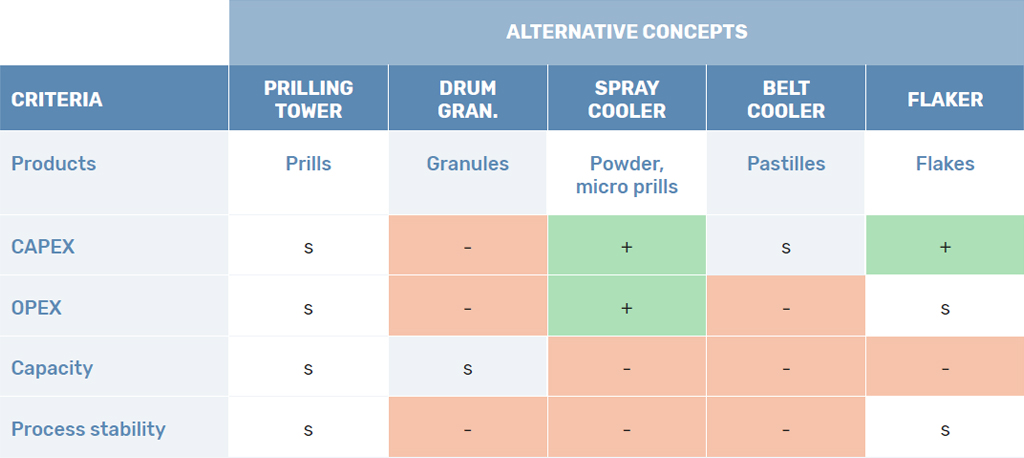
Comparing the Products
Product Particle Size
Both processes result in two very different products, although both spherical and free-flowing. The most apparent difference is the particle size of both products. The particle size in prilling is predominantly determined by the falling height available in the prilling tower. The falling height determines the cooling time of the prill and thus the maximum size. Therefore, limitations in the construction of the tower ensure that the average prill size usually lies between 0.5mm up to a maximum of 3mm. If vibrational technology is added to the priller the particle size distribution can be narrowed to a minimum deviation.
In granulation, the particle size is dominated by the residence time in the granulator. The longer the layers are allowed to build up, the larger the granules become. This allows for granules to grow as big as 10mm. However, the PSD is harder to control for larger granules, as not all the granules undergo the same process in the granulator and some are put into contact with more melt [4].
Product Strength
The biggest advantage of granules is the higher crushing strength of the granules with regards to the prills, due to the addition of a binding agent during granulation and the formation of a cavity in larger prills. The trends of crushing strength for urea can be seen in Figure 1.
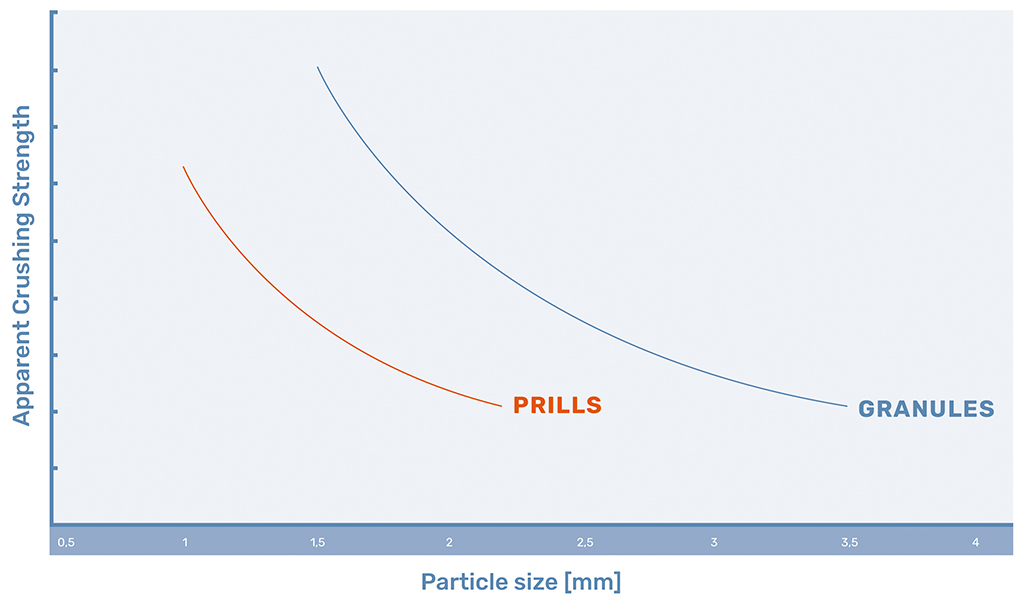
In prilling, after the droplet is formed from the prilling machine, the solidification of the melt starts. At first, the prill solidifies at the interface between the melt and the air, forming a shell of solidified melt that moves inward. However, there is a difference in density between the liquid melt and the solidified prill.
Usually, the solidified prill will take in a smaller volume than the liquid droplet. As the solidification propagates, the prill needs to shrink somewhere. As the shell is already formed, the prill will shrink in the middle, forming a cavity. This core makes for a porous structure of the prill. The bigger the prill becomes, the bigger the cavity in the core of the prill.
In granulation, this porous structure is avoided by the consecutive layer created by the melt and granulation agent. Any hollow areas on the shell of the granule are filled by the next layer and a solid crystal structure is formed. However, this granulation process does require the addition of a granulation agent. This additive helps the formation of a stronger structure. Both processes are shown in Figure 2.
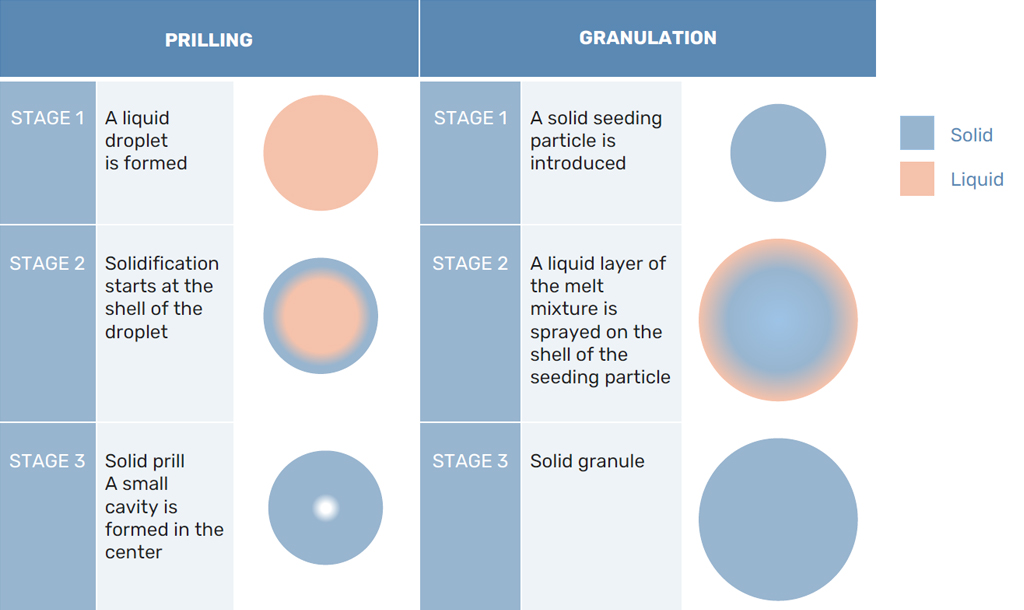
Product Purity
Prilling is a process where melt in is melt out, leading to a product with the highest purity. For a granulation process to run smoothly the addition of a binding agent is necessary. The goal of the granulation plant is to remove as much of the binding agent as possible, but a fraction will always remain present. This can be considered a benefit for prilling, as a binding agent can be added optionally but is not necessary and a pure product can be achieved.
Comparing the Processes
Process Costs
A general rule of thumb is that the initial investment for a granulation plant is three times higher than a prilling tower with the same capacity. A prilling tower can be operated in two different configurations, a version where a natural draft forms the countercurrent airflow and a one where a forced draft is induced by a fan. Natural draft is formed due to the temperature difference between the top of the tower where the melt enters and the bottom where air enters. A higher capacity of melt will lead to a higher temperature difference and subsequently to a higher airflow. The natural draft prilling tower has very little moving parts and is relatively cheap to build and operate. A prilling tower with forced draft can decrease the tower height needed, but in general leads to higher capital and operational expense needed.
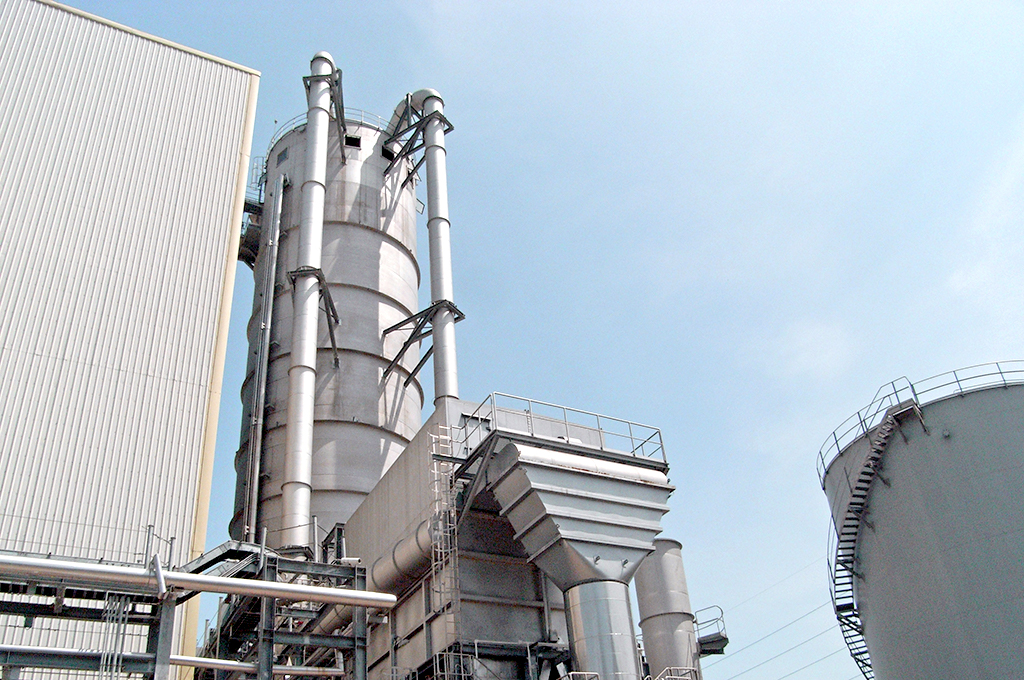
A fluidized bed or rotary granulator requires a larger investment, as it is a more complex process to construct and operate than prilling. There are multiple moving parts and nozzles needed to operate the process.
Process Control
In general, a prilling tower is a more robust and easier process to control than a granulation process. The main benefit of prilling towers for a plant finishing section is the high degree of self-control. The prilling bucket can handle fluctuations in the melt, as the rate of flow out of the bucket is a function of the flow in. Also, as mentioned before, when the flow of melt is increased, the airflow in changes accordingly due to the temperature difference. In addition, as high-quality prilling systems have two buckets, changeover can be done with minimum downtime, leading to a highly robust process [5].
The more complex granulation process usually is harder to control as there is more equipment moving. Also, although we have acquired significant knowledge over the last couple of years, the complex nature of the granulation process and the modeling and operation of granulation plants are hard and, in some cases, still largely based on empiricism, leading to high waste ratios and, by extension, high recycle rates [6].
Process Emissions
In general, the emissions from a prilling tower are considered higher than those generated during granulation. There is a larger gas stream that needs to be treated before it can be either recycled or ejected out of the tower. After treatment, the gas is just as clean as compared to the waste streams of the granulation plant.
However, because the melt is deposited in layers on the seed particles, the residence time of liquid melt is minimal. If a product with a high vapor pressure is to be finished, more product will evaporate in the prilling tower than in a granulation process. The longer the product is liquid, the more of the melt will evaporate, leading to higher losses and dust formation in prilling, which need to be treated.
Conclusion
In the introduction, the question was raised what the difference is between the granulation and prilling, its associated products, and what both can learn from each other. While both products form spherical particles, there are a lot of differences. Prills form smaller, more monodisperse particles, where no additives are needed. Granules on the other hand form bigger and stronger particles, which are more resistant to wear caused by transportation and can homogeneously be blended with other granules based on particle size.
On the process side, prilling, without any precautions, generates more emissions than granulation. However, it provides a much cheaper, less complex, and robust system and can be operated with lower energy consumption. In conclusion, prilling is a more suitable process when a cheaper, monodisperse and pure product is needed, while granulation is better equipped to produce more expensive, larger, and stronger particle which can be better transported.
Overcoming the drawbacks of prilling is the main quest of Kreber, to provide a robust and energy-efficient solution for the finishing of industrial melts. The prill strength and size, the overall emission of the prilling process, and a monodisperse prill distribution are just a few of the challenges our researchers cope with every day. If you want to be a part of our journey towards the perfect prill, we are happy to help you.
References
- Harrison, David. Dream Lead to Invention. Bristol Times, 26 November 2002.
- Watts, Williams. Small Shot. 1347 United Kingdom, 10 December 1782.
- Griffin, Curtis. History of Granulation and State of the Art Granulation. Tampa FL : PegasusTSI, 2015.
- Rahmanian, Nejat, et al.Urea finishing process: Prilling versus Granulation, Procedia Engineering 102, pp. 174 - 181, 2015.
- Van 'T Land, C. M. Industrial Crystallization of Melts. Boca Raton : CRC Press, 2004.
- Al Alaween, W. H., Mahfouf, M. and Salman, A.D. Predictive modelling of the granulation process using a systems-engineering approach. Sheffield, UK : Powder Technology, 2016.
- Lide, D.R. CRC Handbook of Chemistry and Physics. 81st Edition. Boca Raton : CRC Press LLC, 2000.
- Baboo, P. Energy saving and polution control in urea plant through prilling tower and other equipments. 7, Vijaipur : International Journal of Engineering Trends and Technology, Vol. 36, 2016.
- Brouwer, M. ureaknowhow, 2015.