Las diferencias entre prilado y granulación
Desglose y Comparación de dos Tecnologías de Acabado Importantes.
La elección de la tecnología de solidificación adecuada puede ser el factor decisivo, no sólo para los costes de inversión u operacionales, sino también para la consistencia de la calidad de su producto. Con la información adecuada, usted podrá tomar las decisiones correctas. Por eso vamos a comparar dos importantes tecnologías de acabado: prilado y granulación.
Introducing the technologies
El Prilado: Vayamos a los Orígenes
El inventor del método de prilado fue un fontanero del Reino Unido llamado William Watts. En 1782, descubrió que haciendo salir plomo fundido por un pequeño agujero desde una gran altura, las gotas de plomo, al caer, se solidificaban y formaban perdigones esféricos.[1] Dichos perdigones tendrían un tamaño similar y una forma más esférica que los obtenidos por los métodos de producción al uso en aquellos tiempos.
El principio básico del proceso de prilado no ha cambiado mucho desde que William Watts lo descubrió en 1782.[2] La principal diferencia es que hoy en día se usa una máquina de prilado en la que se producen grandes cantidades de chorros de líquido al forzar el material fundido a través de una boquilla, tras lo cual el chorro se desintegra produciendo gotitas finas. La máquina de prilado proporciona un mayor control de la desintegración del chorro y consecuentemente mejor calidad y tamaño del producto. Además, puede circular aire por la torre y el polvo puede recogerse en instalaciones de filtros o mediante el uso de depuradores, lo cual hace que el proceso sea más seguro. Para más información sobre los principios básicos del prilado, lea el siguiente artículo: significado de prilado y definición de prill.
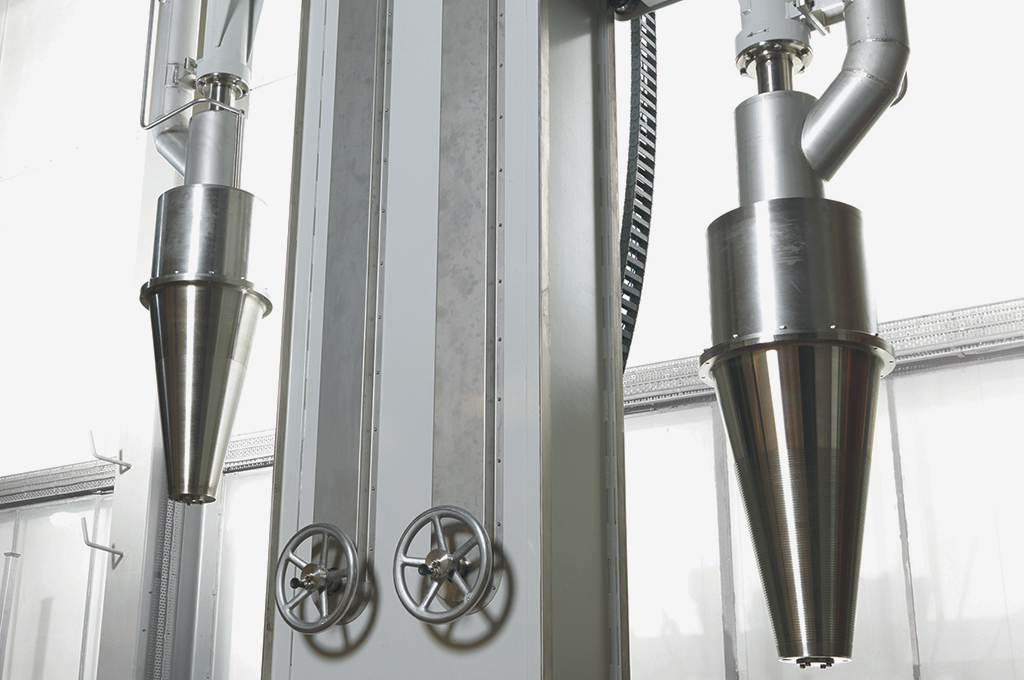
Granulación: Tecnología Prometedora.
La tecnología de granulación ha emergido en la historia reciente como una tecnología prometedora para la fabricación de fertilizantes de alta calidad. El granulador de amonio fue descubierto en 1965 y patentado por Frank Nielson. Nielson trabajaba para la Autoridad del Valle de Tennessee (TVA) (Tennessee Valley Authority) que, en parte, pasó a convertirse en el Centro Internacional de Desarrollo de Fertilizantes. El trabajo llevado a cabo por la TVA tuvo como resultado la emergencia de un competidor para el proceso de prilado en el acabado a gran escala de los Fertilizantes Químicos [3].
En el proceso de granulación, pequeñas partículas se unen para formar un gránulo. Tanto la masa fundida como el aglutinante se introducen en el granulador como una nube de pequeñas gotas. Las pequeñas partículas de nucleación crecen a expensas de la nube de gotas hasta que se forma el gránulo deseado. El tambor giratorio y las altas velocidades del aire aseguran la eficiente humidificación, secado y transporte de energía.
Tras 50 años de innovación en el campo de la granulación y más de 200 en el campo del prilado, ambas tecnologías han evolucionado hasta convertirse en tecnologías de acabado maduras que se utilizan en todo el mundo. Pero, después de tantos años de investigación y desarrollo ¿es posible distinguir entre los diferentes productos? Y, ¿cuáles son las ventajas e inconvenientes de los priladores y los granuladores de última hechura? Y, por último, ¿pueden ambas tecnologías aprender una de otra para evolucionar hacia mejores prácticas de acabado de fertilizantes?
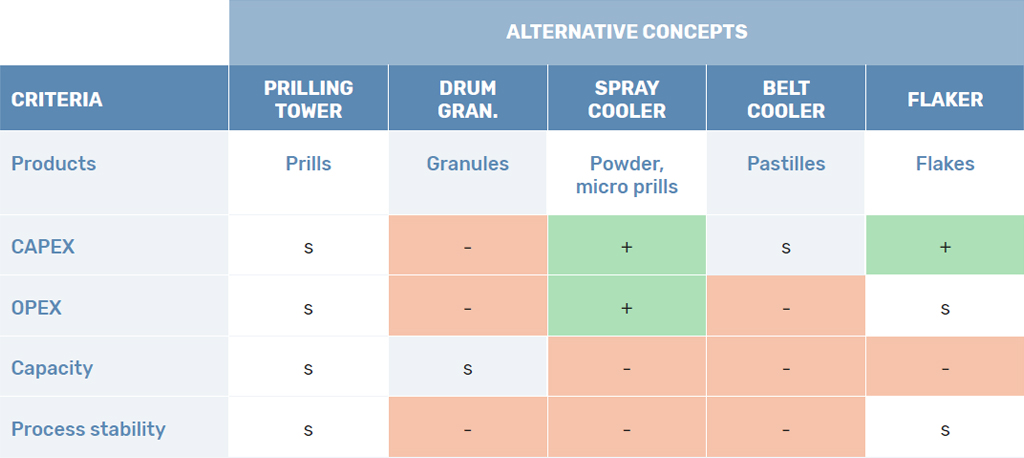
Comparación de los Productos
Tamaño de Partícula del Producto.
Cada uno de los dos procesos produce un producto muy diferente del del otro, aunque ambos productos sean esféricos y de flujo libre. La diferencia más notable es el tamaño de partícula de cada producto. El tamaño de partícula del prilado viene predominantemente determinado por la altura de caída disponible en la torre de prilado. La altura de caída determina el tiempo de enfriamiento del prill y por consiguiente su tamaño máximo. En consecuencia, las limitaciones en la construcción de las torres hacen que el tamaño de partícula medio se sitúe frecuentemente entre un mínimo de 0,5mm y un máximo de 3mm. Si se aplica la tecnología de vibración al prilador, la distribución de tamaños de las partículas se puede estrechar hasta una desviación mínima.
En la granulación, el tamaño de la partícula viene determinado por el tiempo de residencia en el granulador. Cuanto más tiempo se da a las capas para irse añadiendo, más grandes se hacen los gránulos. Esto permite alcanzar tamaños de grano de hasta 10mm. No obstante, la distribución de los tamaños de partícula (DTP) es más difícil de controlar para los gránulos mayores, ya que no todos los gránulos pasan por el mismo proceso en el granulador y algunos están en contacto con más material fundido que otros [4].
Resistencia del Producto
La principal ventaja de los gránulos sobre los prills, es su mayor resistencia a la trituración, debido a la adición del aglutinante durante la granulación y al desarrollo de una cavidad en los prills más grandes. En la Figura 1 se muestra la evolución de la resistencia a la trituración en el caso de la urea.
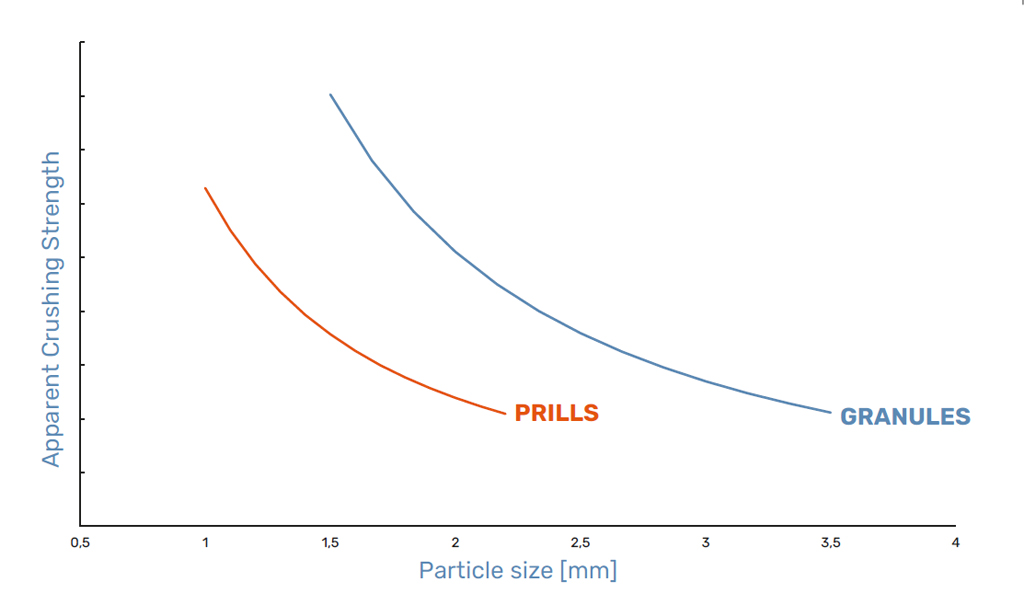
En el prilado, una vez las gotas se han formado en la máquina de prilado, comienza la solidificación. Al principio el prill se solidifica en la interfaz masa fundida/aire, formando una corteza exterior, que crece hacia el interior. No obstante, hay una diferencia de densidad entre la masa fundida líquida y el prill solidificado.
Normalmente, el prill solidificado tendrá un volumen inferior al de la gota líquida. Conforme progresa la solidificación, el prill necesita encogerse de algún modo. Como la corteza ya se ha formado, el prill se encogerá por dentro, formando una cavidad. Este núcleo es lo que hace que el prill tenga una estructura porosa. Cuanto más grande sea el prill, más grande será la cavidad en su núcleo.
En la granulación, la estructura porosa se evita por el proceso de formación de capas consecutivas de masa fundida y agente de granulación. Cualquier área vacía en la corteza del gránulo es rellenada por la siguiente capa y se forma una estructura cristalina. Sin embargo, este proceso de granulación requiere la adición de un agente de granulación. Este aditivo ayuda a la formación de una estructura fuerte. Ambos procesos están representados en la Figura 2.
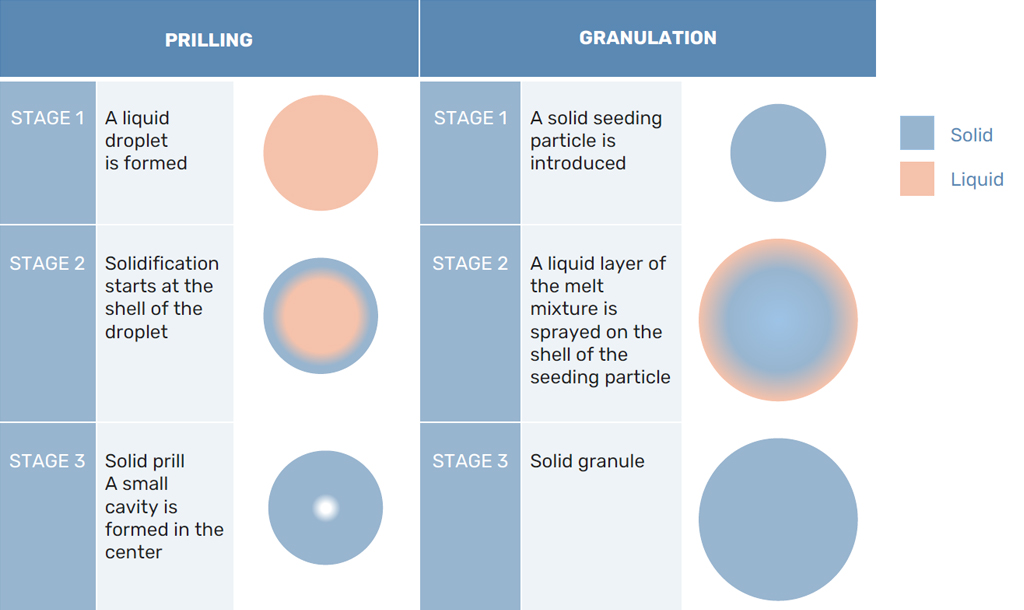
Pureza del Producto
El prilado es un proceso en el que la masa fundida que entra es lo que sale, lo que conduce a un producto de la más alta pureza. Para que el proceso de granulación funcione correctamente, es necesario añadir un aglutinante. El objetivo de una planta de granulación es eliminar en lo posible el agente aglutinante, pero siempre queda una fracción. Esto se puede considerar como una ventaja para el prilado, porque si bien es posible añadir un agente aglutinante, no es necesario hacerlo pudiéndose conseguir un producto puro.
Comparación de los Procesos
Costes del Proceso
Una regla general dice que la inversión original necesaria para una planta de granulación es tres veces mayor que la de una torre de prilado de la misma capacidad. La torre de prilado puede ser operada en dos configuraciones diferentes, una versión en la que el flujo de aire a contracorriente se genera por tiro natural, y otra versión en la que un ventilador genera una corriente de aire forzada. El tiro natural se forma por la diferencia de temperatura entre la punta de la torre, donde entra la masa fundida, y el fondo de la torre, donde entra el aire. Cuanta más capacidad de masa fundida haya, más diferencia de temperatura habrá y, por consiguiente, mayor flujo de aire. La torre de prilado con corriente de aire natural tiene muy pocas partes móviles y su construcción y operación son relativamente baratas. Una torre de prilado con corriende de aire forzada puede reducir la altura necesaria de la torre, pero en general conduce a mayores gastos operacionales y de capital.
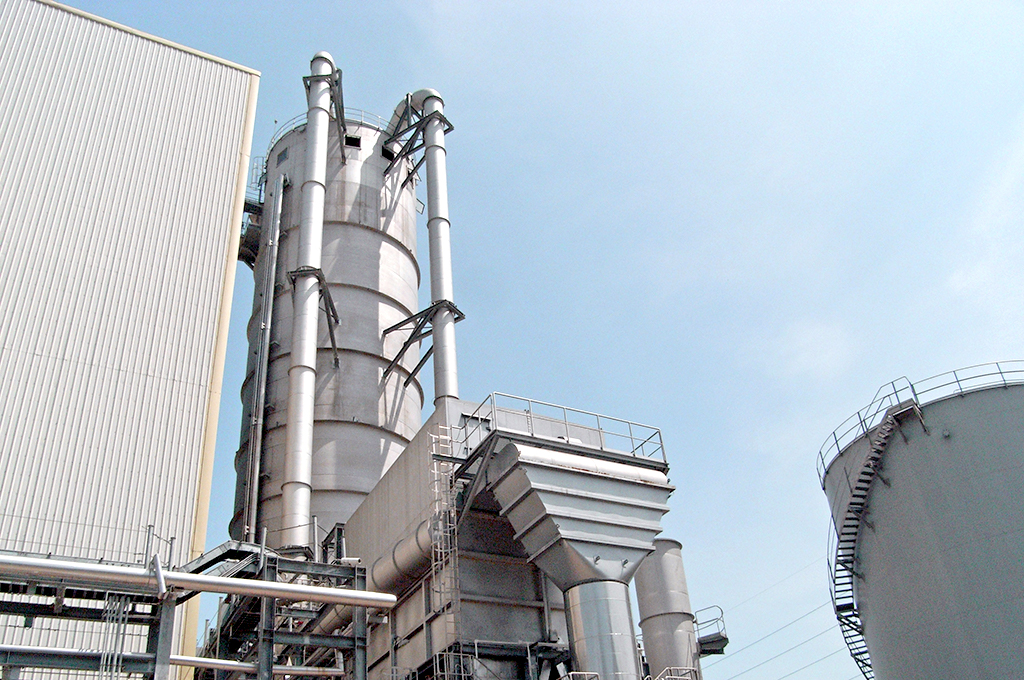
Un granulador de lecho fluidizado o rotativo requiere una inversión mayor, porque los procesos de construcción y operación son más complejos que en el caso del prilado. Se necesitan muchas boquillas y partes móviles para la operación del proceso.
Control del Proceso
En general el proceso en una torre de prilado es más robusto y más fácil de controlar que el proceso de granulación. La mayor ventaja de las torres de prilado para la sección de acabado de una planta es el alto grado de auto control. La canastilla de prilado puede manejar fluctuaciones en la masa fundida ya que la velocidad de flujo de salida de la canastilla es una función del flujo de entrada. También, como hemos mencionado anteriormente, cuando el flujo de la masa fundida aumenta, el flujo de aire se adapta automáticamente debido a la diferencia de temperatura. Además, como los sistemas de alta calidad de prilado tienen dos canastillas, el cambio se puede llevar a cabo con un mínimo tiempo de parada, consiguiéndose un proceso altamente robusto [5].
El proceso de granulación, que es más complejo, es más difícil de controlar porque hay más componentes del equipo en movimiento. También, aunque en los últimos años hemos adquirido mucho conocimiento, la compleja naturaleza del proceso de granulación y el modelado y operación de las plantas de granulación son difíciles y, en algunos casos, todavía se basan, sobre todo, en conocimiento empírico, lo que lleva a una gran proporción de residuos y, por extensión, a grandes proporciones de reciclaje [6].
Emisiones
En general las emisiones de una planta de prilado se consideran mayores que las generadas durante la granulación. Hay una corriente de gas mayor que tiene que ser tratada antes de poderse reciclar o expulsar de la torre. Después del tratamiento, el gas es tan limpio como los flujos residuales de una planta de granulación.
No obstante, como la masa fundida se deposita en capas sobre las partículas núcleo, el tiempo de residencia de la masa fundida líquida es mínimo. Si se tiene que acabar un producto con una presión de vapor muy alta, se evaporará más producto en la torre de prilado que en un proceso de granulación. Cuanto más tiempo esté el producto en fase líquida, más masa fundida se evaporará, lo que llevará a mayores pérdidas y formación de polvo durante el prilado que necesitarán ser tratados.
Conclusión
En la introducción se planteó la pregunta de cuál es la diferencia entre la granulación y el prilado, sus productos asociados, y cuáles son las ventajas de cada uno de estos procesos. Aunque en ambos casos el producto consiste en partículas esféricas, hay muchas diferencias. Los Prills constituyen partículas de tamaño más pequeño y monodisperso, que no necesitan aditivos. Por otra parte, los Gránulos forman partículas más grandes y más fuertes, que son más resistentes al desgaste por transporte y que se pueden mezclar de forma homogénea con otros gránulos en base al tamaño de partícula.
En lo que respecta al proceso, sin la adopción de precauciones el prilado genera más emisiones que la granulación. No obstante, ofrece un sistema mucho más barato, menos complejo y muy robusto que puede ser operado con bajo consumo energético. En conclusión, el prilado es un proceso más adecuado cuando se necesita un producto barato y puro, con un tamaño de partícula monodisperso, mientras que la granulación es más apta para producir partículas más grandes y más fuertes que se pueden transportar mejor, pero cuyo precio es más elevado.
La principal misión de Kreber es superar los inconvenientes del prilado, para ofrecer una solución robusta de bajo consumo energético para el acabado de las masas fundidas industriales. La resistencia del prill y su tamaño, las emisiones del proceso de prilado en su totalidad, y una distribución monodispersa del tamaño de partícula son sólo algunos de los retos en los que trabajan nuestros investigadores en el día a día. Si usted quiere caminar con nosotros hacia la consecución del prill perfecto, estaremos encantados de colaborar.
Referencias
- Harrison, David. Dream Lead to Invention. Bristol Times, 26 November 2002.
- Watts, Williams. Small Shot. 1347 United Kingdom, 10 December 1782.
- Griffin, Curtis. History of Granulation and State of the Art Granulation. Tampa FL : PegasusTSI, 2015.
- Rahmanian, Nejat, et al.Urea finishing process: Prilling versus Granulation, Procedia Engineering 102, pp. 174 - 181, 2015.
- Van 'T Land, C. M. Industrial Crystallization of Melts. Boca Raton : CRC Press, 2004.
- Al Alaween, W. H., Mahfouf, M. and Salman, A.D. Predictive modelling of the granulation process using a systems-engineering approach. Sheffield, UK : Powder Technology, 2016.
- Lide, D.R. CRC Handbook of Chemistry and Physics. 81st Edition. Boca Raton : CRC Press LLC, 2000.
- Baboo, P. Energy saving and polution control in urea plant through prilling tower and other equipments. 7, Vijaipur : International Journal of Engineering Trends and Technology, Vol. 36, 2016.
- Brouwer, M. www.ureaknowhow.com, 2015.