Spray Congealing
Spray congealing is an efficient process utilized in the manufacturing industry for the production of solid powders. This innovative technique involves atomization, rapid cooling, and solidification to create uniform and high-quality solid materials.
Atomization
The spray congealing process begins with the precise atomization of the liquid material. The liquid is heated to a specific temperature and then transformed into fine droplets using a high-pressure nozzle system. This atomization stage ensures that the liquid is converted into small, uniformly-sized droplets, setting the foundation for consistent particle formation.
Rapid Cooling and Solidification
The atomized droplets are introduced into a controlled environment, typically a temperature-controlled chamber. Within this chamber, the droplets come into contact with a cold gas stream or a cooling medium. The sudden exposure to the cool environment leads to rapid cooling and solidification of the droplets, transforming them into solid particles. The resulting particles exhibit spherical shapes, and uniform sizes.
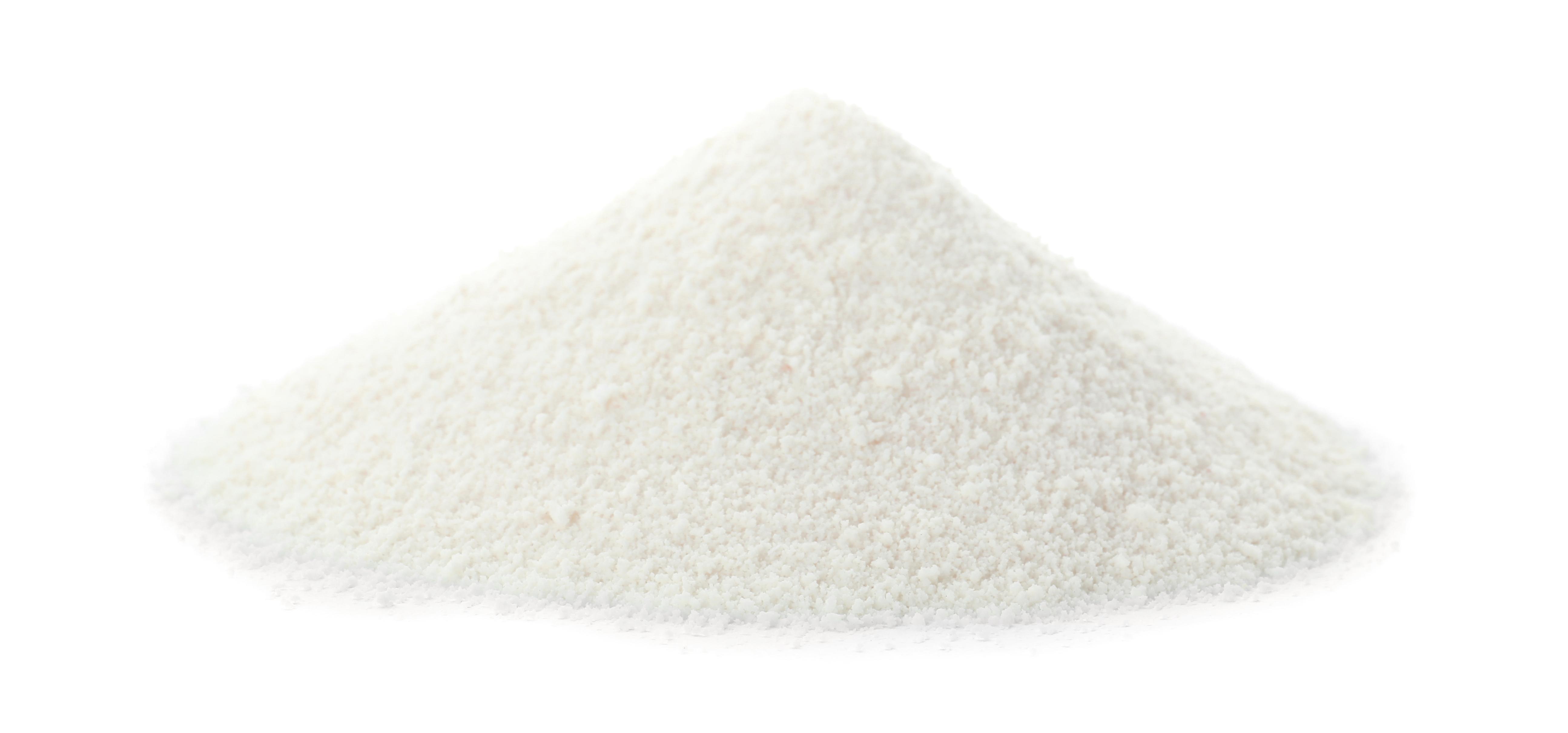
Spray congealing enables the production of spherical particles with precise and uniform sizes. This uniformity enhances product quality and performance, making spray congealing ideal for applications where consistency is critical.
Our equipment is easy to operate, due to our well defined process operating parameters. Furthermore, the low amount of rotating and intricate parts result in a reliable process, giving the client an overall low operational and maintenance cost.
The process is particularly advantageous for encapsulating sensitive or volatile substances. By solidifying the liquid droplets quickly, spray congealing can protect and preserve the integrity of sensitive components during the manufacturing process.
Spray congealing allows for the incorporation of multiple ingredients into compounded particles, facilitating the creation of composite materials with tailored properties. This flexibility enables the development of advanced materials with enhanced functionalities.
Thanks to a constant stream of technical innovations, such as state-of-the-art air inlet filtration and closed loop operation, emissions can be cut to virtually non existing.